During a Feb. 13 visit to British Columbia, federal Liberal leadership candidate Mark Carney vowed to help lower building costs and get more new homes built across Canada.
He was at the University of British Columbia (U小蓝视频) Smart Structures laboratory, where he was briefed on new technologies that could help tackle the country’s housing shortage.
“This is a time to build,” the former Bank of Canada governor said in a media statement about his visit.
“We will catalyze enormous private investment to build millions of new homes.”
Lucky for him, U小蓝视频 Smart Structures knows a thing or two about building.
The research institute is pioneering new construction practices, including modular, robotic and AI-driven methods. And with Ottawa’s aim to build 3.9 million new homes by 2031, the lab’s innovations could help Canada get there sooner rather than later.
“We can ensure these new-generation buildings are smarter, more resilient, more carbon-neutral and, in fact, more economical to build,” said Tony Yang, professor of structural and earthquake engineering in U小蓝视频’s civil engineering department.
“If everything works out well, this could be the technology in [Carney’s] mind to counter the tariffs, to show that we can really ramp up the production capability for housing in Canada.”
With public and private funding sources, U小蓝视频 Smart Structures is developing homegrown research that can be tailored to the 小蓝视频 housing market. Research from other parts of Canada and the world may not necessarily be appropriate for the local context, given the province’s unique seismic hazards, for example.
The lab is exploring different aspects of sustainable construction, and has its hands in many niches, ranging from timber construction and volumetric modular construction, to structural fuses and artificial intelligence.
“We are developing the next-generation technology to allow Canadian construction to go faster,” said Yang. “We are probably the leader in the area, clearly in Canada and maybe also in the world.”
Conventional construction is time-consuming and requires a significant amount of human labour, he said. In addition, construction quality can be inconsistent and can be affected by adverse weather and other factors.
However, the U小蓝视频 team said it believes advanced modular and robotic construction can achieve faster construction, better quality control, less environmental impact, lower operating costs, less waste and fewer injuries.
The crown jewel of the team’s research is a state-of-the-art method that allows robotic arms—affixed to ground vehicles—to grasp structural components and place them in specific positions to form whole structures.
Yang said the goal is to automate construction equipment. The robotic equipment resembles existing construction machines and can be controlled by algorithms, thus requiring minimal or no human involvement.
“We are developing the next-generation structure system that can be efficiently connected and put together almost 100-per-cent autonomously by robots,” he said.
“We call them ‘robots’ but they are very similar to construction machines that you see on any construction site. We just make them smarter. They are the muscles; we are just putting the brains behind them to make them automated, to upgrade them.”
Assembly of building components would occur partly off-site in factories and partly on construction sites themselves. The process is expected to reduce the amount of construction waste, and it would also incorporate more environmentally friendly structural materials with less embodied carbon, he said.
How much time could the new technology save? Yang pointed to China, where he said a 15-storey building can be constructed “from nothing to fully operational” in just one week, thanks to prefabrication and a surplus of labour. He said he believes his lab’s technology could result in similar time and cost savings on this side of the Pacific Ocean, where a project takes years from start to finish.
The goal of automation is not to replace construction workers, he said, but to deploy them more efficiently and productively. In the future, construction workers would ideally perform higher-level decision work, such as assigning and managing tasks, rather than intensive physical exertion.
Yang also noted 小蓝视频’s shortage of skilled construction labour—one of the problems solved by his new technology.
According to an April 2024 report, the 小蓝视频 Construction Association projected a deficit of 6,600 skilled workers by 2033. The same report also noted that the number of tradespeople in the industry has fallen by seven per cent—167,300 people—over five years, and that the average company size has contracted by 15 per cent over the previous five years to an average of 5.97 skilled trade workers per firm.
The autonomous methods being developed by U小蓝视频 Smart Structures can be adapted to construction projects of all sizes, helping to alleviate these critical needs. Even tall condo towers can be erected using these innovative methods; the lab has developed a fully robotic crane, which can be operated autonomously or semi-automatically, Yang said.
His team has already tested the assembly of full-scale components and aims to create a full-scale building in the next stage. Challenges facing the researchers include small imperfections in the assembly of structural components by the robotic equipment, which can be rectified with the use of better sensors and controls.
The U小蓝视频 team said the technology can be commercialized and scaled up in the next four to five years. They have not yet decided whether to make their research and intellectual property free for anyone in the world to replicate and monetize.
“We will be keen to collaborate with different entities,” Yang said.
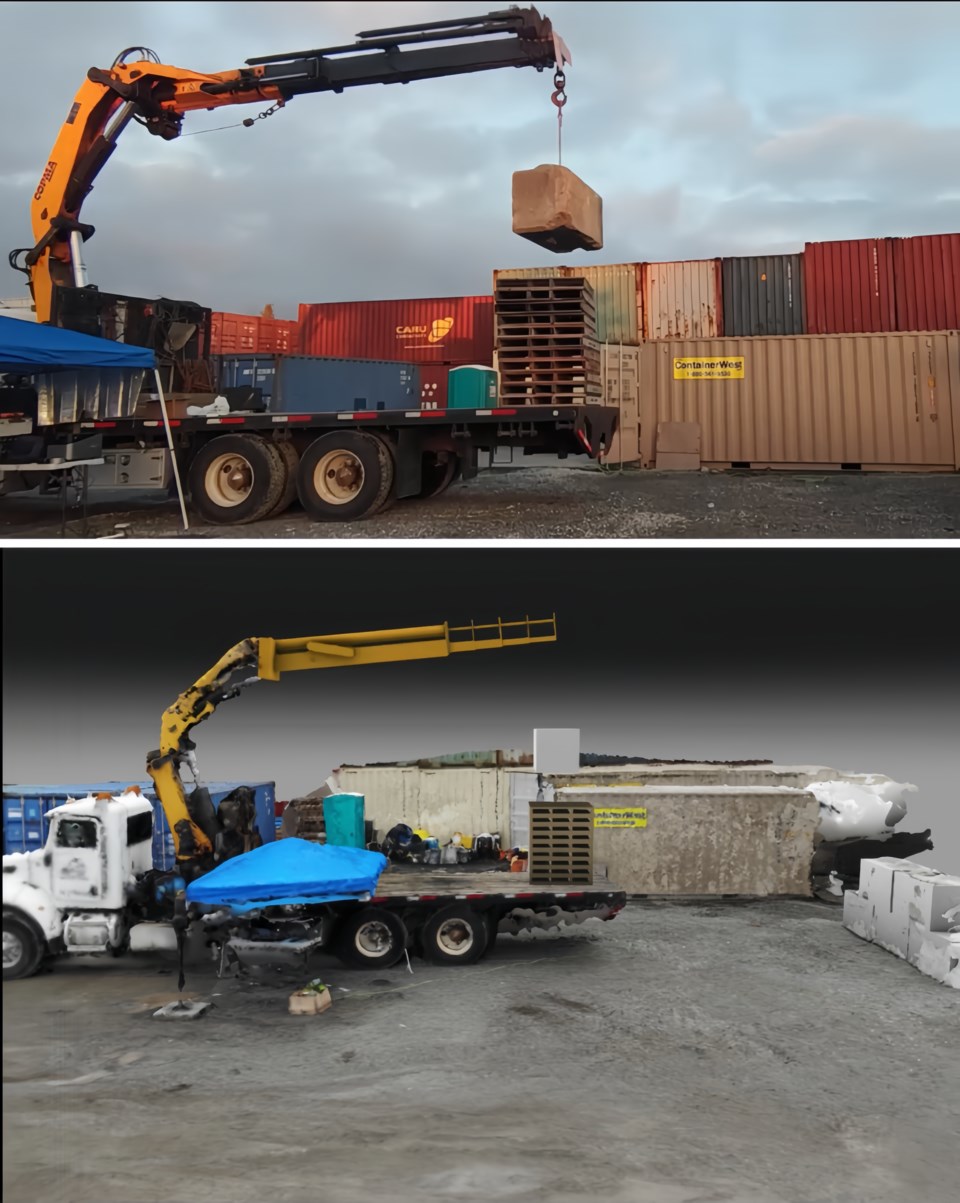
The lab has already partnered with Rogers Communications Inc. to develop next-generation communication protocols. Rogers would provide connectivity services to construction sites and equipment, so robotic equipment could be deployed to construction sites in remote areas with few skilled workers, and operated remotely from hundreds of kilometres away.
“We are very keen to work with industry, if anyone is interested in working with us to take it to the next level to commercialization,” Yang said.
U小蓝视频 Smart Structures is also working with several construction firms and plans to build out a production line and supply chain to allow its new methods to be implemented and tested on a larger scale.
“We hope the technology can be used by the industry ASAP,” Yang said. “We just need to start scaling up to help address the housing supply challenge.”